Business
ESG
Applying Environmental, Social, and Governance (ESG) management in the textile industry involves adopting strategies that address sustainability, social responsibility, and ethical governance. Here are five ways to implement ESG management in our business
- 1. Environmental Sustainability Practices:
- Use eco-friendly materials such as organic cotton, recycled fibers, and low-impact dyes.
- Implement energy-efficient processes and use renewable energy sources like solar and wind power.
- Minimize waste by adopting circular economy principles, such as recycling textile waste and designing for recyclability.
- Track and report greenhouse gas emissions, setting targets for reduction.
- 2. Social Responsibility Initiatives:
- Implement fair wages, safe working conditions, and reasonable working hours in line with international labor standards.
- Provide training and development opportunities for employees to enhance their skills and career prospects.
- Promote diversity and inclusion within the workforce, ensuring equal opportunities for all employees.
- 3. Ethical Supply Chain Management:
- Establish long-term relationships with suppliers who share the company’s ESG values.
- Require suppliers to comply with codes of conduct that cover labor rights, environmental practices, and ethical standards.
- Monitor and audit suppliers regularly to ensure compliance with ESG criteria.
- Encourage suppliers to adopt sustainable practices, offering support and incentives for improvements.
- 4. Sustainable Product Innovation:
- Invest in research and development to create sustainable textiles and garments with a lower environmental footprint.
- Develop products that are durable, recyclable, and made from renewable or recycled materials.
- Collaborate with industry partners and stakeholders to drive innovation in sustainable textiles and fashion.
LEAN SYSTEM
Applying the LEAN system in a manufacturing plant involves streamlining operations to enhance efficiency, reduce waste, and improve overall productivity. Here are three effective ways we implement LEAN principles
-
Value Stream Mapping (VSM):
Create a detailed visual map of all the steps involved in the production process to identify and eliminate waste.
-
Just-In-Time (JIT) Production:
Implement JIT production to align manufacturing output with customer demand, reducing inventory costs and minimizing waste.
-
Continuous Improvement (Kaizen):
Promote a culture of continuous improvement (Kaizen) where all employees are encouraged to contribute ideas for improving processes.
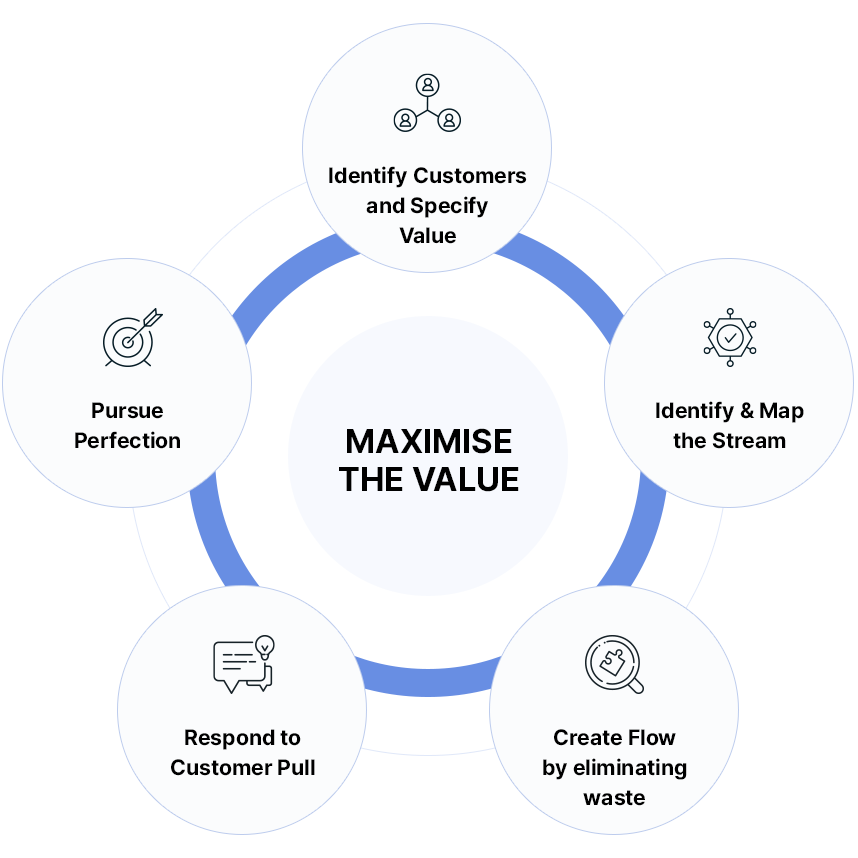
Smart Factory
Our company aims to transition to a smart factory in all aspects of production process and management, and recently introduced a new MES system to collect, analyze, and evaluate real-time production data to understand the production status intuitively and instantly, showing a 15% improvement in efficient productivity.
- Visibility
- Real-Time Sewing Line
- Balancing
- Intuitive Real-Time Analysis
- Prompt In-Line Feedback Motivation to all
- QC Productivity
- Minimize Loss & Defect
- Improve Work Process
- Real-Time QC (TQC)
- Efficiency
- Management Cost Saving
- Enhancing Collaboration
- Miracle Returns on
- Investment
- Usability
- Plug & Play Installation
- No hassle cables
- Expendable and Flexible
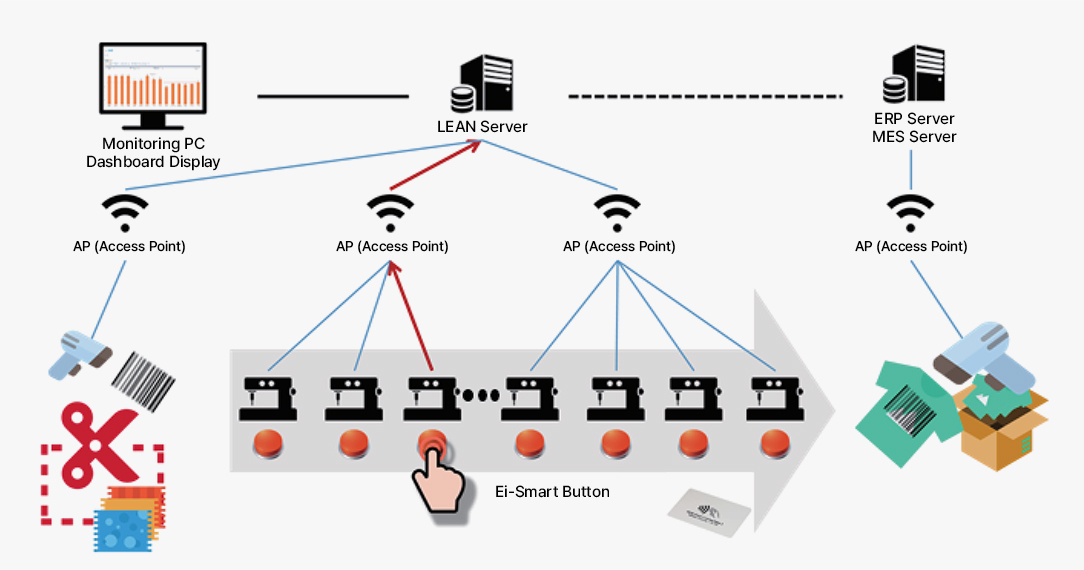